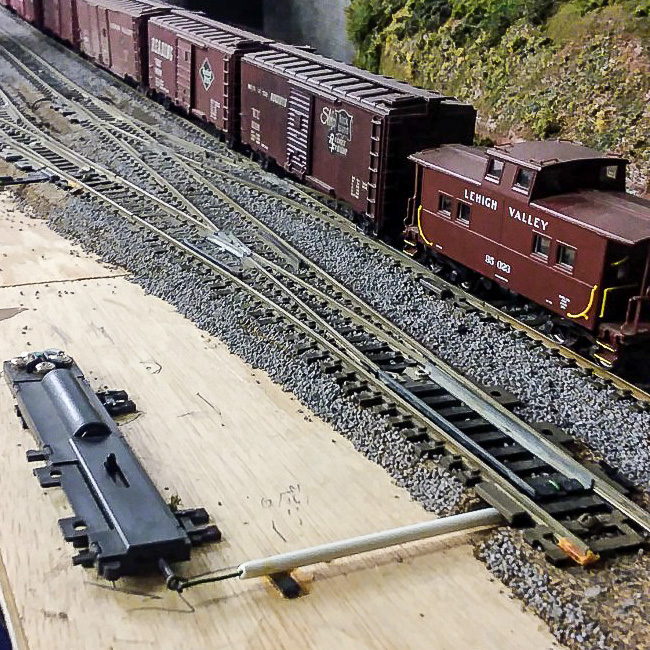
From John Pursell
I use Atlas switch machines on my layout. They’re reasonably priced, reliable, and available just about everywhere. I’ve even gotten used to the “buzz-clack” sound as one of them operates. What I’ve never gotten used to, though, is the big, honkin’ piece of black plastic that houses the solenoid. It lays right by the track and, in my opinion, bears no resemblance to anything prototypical. Because of this, I’ve devised ways to hide or disguise them.
I am aware of Atlas’s switch machines for “under table” mounting. I’ve used them in the past and they work well. But as my age advances and bad knees become more of a fact of life, I want to make as few trips as possible under my layout. I’ve decided to keep switch machines above ground, so to speak. I also know that Atlas includes a little piece of black plastic that allows you to mount the machine a bit further away, but even that’s not far enough for me. I prefer to have at least 3 to 4 inches between a turnout and the machine to allow for my coverings.
The first thing I do is work out a way to mount the machine at least a few inches away from the turnout and create the connection. When mounting them in this way, Atlas’s “left/right hand” switch machine designations do not matter because those cast-on track connections won’t be used.
My method uses a piece of green florist wire that is about 3/4 inch longer than the distance between the center of the turnout’s points and my Atlas switch machine throw bar’s location. First I measure 3/8 inch from one end of the wire and bend it up 90 degrees. Then I measure 1/8 inch from the tip on that bent end and bend it another 90 degrees, perpendicular to the first bend. Fit it into the hole on the turnout’s throw-bar. It should now extend, perpendicular to the track section, underneath the throw-bar. I do this before I mount the turnout on the roadbed.
Trim the roadbed under the throw-bar to allow the wire to freely move under the points. Note that the wire must also lay flat on top of the throw-bar so a passing coupler trip pin doesn’t get snagged.
It may take some trial and error to get this right. I use code 100 track and the measurements for bending could be different for different codes of rail or other manufacturer’s track. The measurements above are estimated. Florist wire is inexpensive. If it’s not correct, I toss it and do another.
Next, with the wire protruding out from the turnout to where the machine mounting spot will be I run the wire through a length of plastic tube that will fit between the roadbed and the machine. This allows me to cover the connection, preventing scenic material and adhesives form interfering with its movement. At the switch machine, the wire is bent around the actuating lever and squeezed down using pliers to reduce any play.
Holding the switch machine in it’s mounting spot, I check to see if everything works. In general, I keep the switch machine and turnout parallel to one another. When it functions smoothly, I permanently attach the switch machine and turnout with adhesive caulk. This will hold it, more or less, permanently. Since caulk always retains some resiliency, I’ll be able to replace it (with perhaps some small effort) if necessary. On occasion, I’ve mounted the machine on a small piece of cork roadbed, which puts it at the same height as the turnout. Using this method allows me to run a longer actuating (floral) wire under an adjacent track inside the plastic tube.
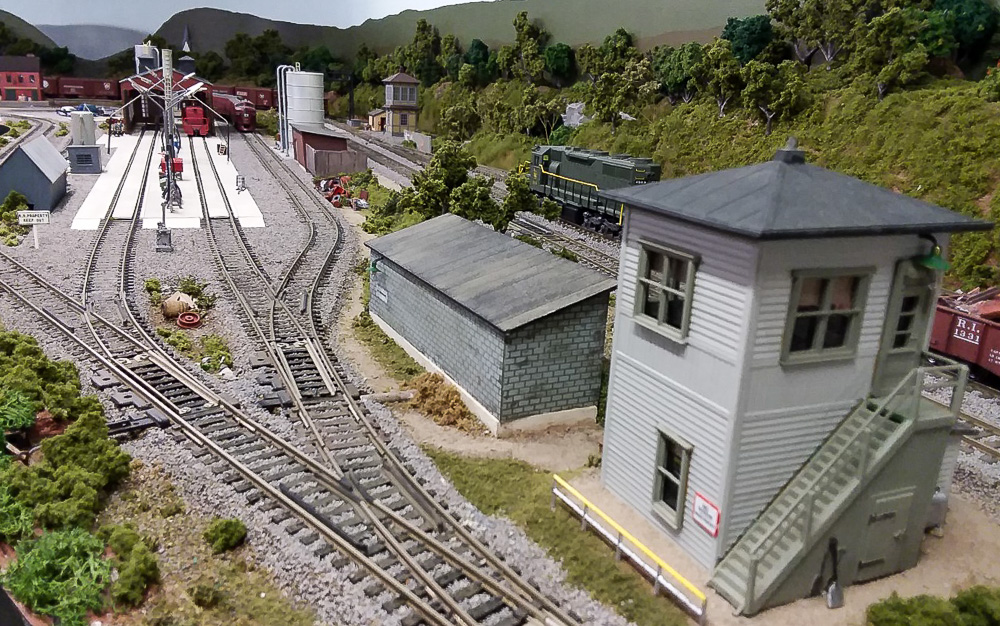
Disguising the machine consists of multiple methods. All of this should work for other types of switch machines. One advantage of Atlas machines is they are fairly flat. This helps with hiding them. The accompanying photo shows several of the ways I’ve done this. A small building with a slot for the wire to go through can be whipped up in minutes. Leave the building loose for adjustments or repairs. I also hide them behind trees or ground foam bushes. If going this route, I cover the actuator pin opening in the machine while gluing, painting, or working with foam. I’ve can also made a small knoll out of carved foam to fit over the machine, covering the knoll with ground foam, grass, and weeds to blend in the rest of the scenery. If this knoll is by an industrial area, I would cover it with mixed, small pieces of junk to resemble a scrap pile. Since the machines are flat, I’ve also hidden them behind fences, extend an inch or two beyond the edges of the machine, completely hiding them. Fences are often good if there’s just no room for anything else.
Above is the Easton engine terminal on my Lehigh Valley RR, where six Atlas switch machines are hidden. Clockwise from the left: #1 inside the gray shed, #2 inside the red shed, #3 behind the hillside, #4 behind the bushes, #5 behind the block shed and #6 behind the shrubs across from the block building.
However, there are “worst case” scenarios. What if there’s simply no space for mounting the switch machine other than right by the track as Atlas intended? If I can’t hide it, I camouflage it. This is easily done by painting the machine (below) the same color as the ballast, making it much less noticeable. Oddly enough, over the years I’ve met many modelers who have simply never thought that you could paint the switch machine. As long as paint doesn’t get into the operating area it works fine. Depending on the surrounding scenery, I recommend gluing a few small pieces of foam on the sides to help the machine blend in better.
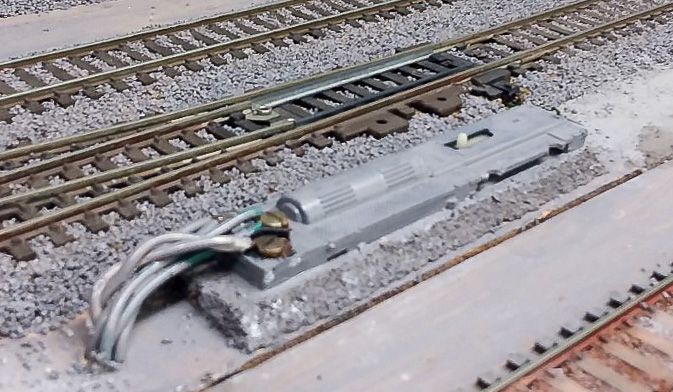
So that’s how I do it. It’s not difficult and allows me to keep using my preferred brand of switch machine. Try it and see if you like it. I assure you, your back and your knees will thank you!