by Don Florwick
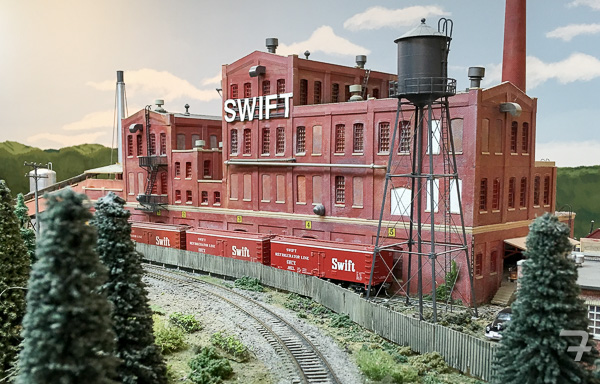
This January fourteen members of the South Mountain Division responded to an invitation from Mat Thompson, MMR to operate on Mat’s exquisite Oregon Coast Railroad. We had a wonderful time and thank Mat for sharing his wonderful railroad with us. This was my 4th visit to Mat’s railroad. This time Mary Miller, MMR and I were assigned to work at the Swift Packing Plant. We had a blast, hence this article.
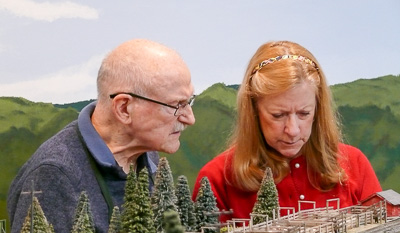
Mary and I begin our session at Hoyt Street Yard. The yardmaster showed us our Oregon Coast train. Behind our switcher we find a cut of 8 cars billed to the packing plant consisting of 4 empty reefers, 3 loaded stock cars, a box car of packing material, and a caboose.
The Swift Packing Plant is located along the railroad between the Hoyt Street Yard and Willbridge, 2 railroad miles away. As an extra, all scheduled trains are superior to us and we have to carefully pick our time to leave the yard for our run on the single track main to reach the plant. We receive a clearance from the yardmaster and, after checking our timetable for superior trains, we pick our way out of the West end.
Before reaching the plant siding we notice a double ended siding along the main, used for outbound traffic to be picked up by passing freights or another switcher out of Hoyt Street. This day, a yard switcher will service the siding during our 8 hour shift; taking our outbounds while delivering more empties and loads.
Just short of Willbridge, we pull our string slowly ahead until the caboose clears the siding switch and glide to a stop. With the switch lined for the plant, we back our string of cars slowly down the siding, clearing the main.
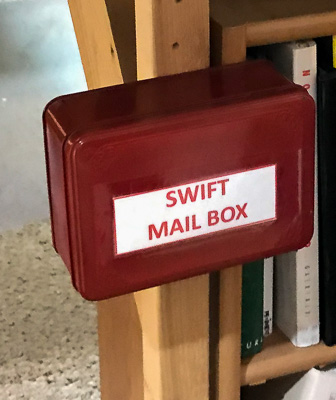
A mailbox at the plant holds special instructions for us, from the customer, so that cars are spotted correctly and in a timely manner, ensuring plant operations proceed smoothly despite our inexperience with this job.
Reading the instruction provided by plant management, we discover that it takes 21 minutes to unload a stock car at the stock pens on track-2. It takes about an hour to load a clean chilled reefer at the plant on track-2, and about 2 hours to ice and chill a block of reefers on track-1 at the icing dock. We also note the track diagram provided so we can find our way among the maze of tracks at the plant.
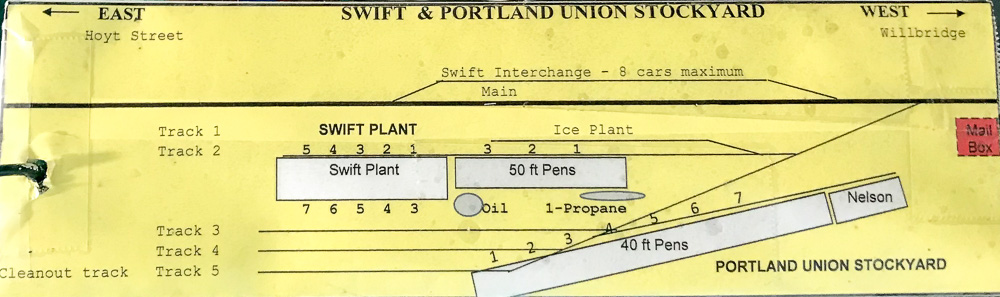
Looking at the diagram, we note that track-3 runs along the back where supplies are offloaded for the packing plant. Track-4 is a service track and track-5 is the cleanout track for reefers. There also is a short runaround track on the ladder between tracks-3 & 5. Note the presence of another stock yard on the property. We were pleased to see there was plenty of head room on the lead to switch the plant without fouling the mainline.
Let’s get started spotting the 8 cars we brought to the plant this morning. You recall we boldly backed into the plant without thought, to clear the main while we looked over our instructions and developed a plan for our first service switch. At the plant we found 1 reefer loaded on track-2, at door-5 and 3 reefers iced, chilled and waiting at the ice dock on track-1. We noted there was one empty box car at door-5 on track-3 and a loaded tank car of tallow spotted near the oil tank, billed outbound.
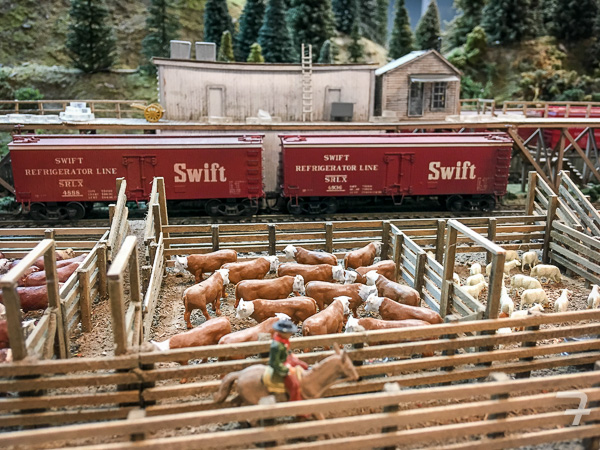
Once oriented, we devise our plan. Here is what we did. First, we pulled our string forward to clear the track-4 switch, then we backed onto track-4 to drop our caboose. Pulling forward to again clear the switch we lined it for the ladder and backed our 4 reefers onto track-5, the cleanout track, and cut away. We then left the remaining 3 loaded stock cars short of track-2 and moved to track-1 where we pulled the 3 iced reefers over to track-2 and shoved them down to doors-1, 2, & 3 for loading.
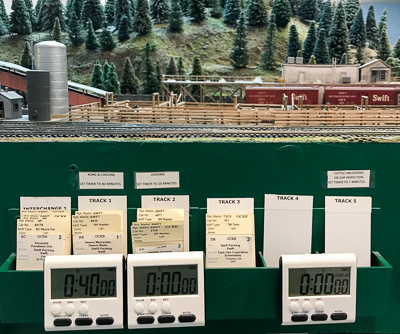
There were three timers provided for our convenience so we set one for 20 minutes. That would use exactly 1 hour of the 3:1 fast clock time for loading. We then came back to the lead and grabbed the 3 loaded stock cars and swung them over to track-2 at the pens. We had 40 foot stock cars so each had to be individually positioned at the unloading shoots that were spaced for 50 foot cars. Once in position we set the second timer to 7 minutes, giving us 21 minutes of fast time for unloading.
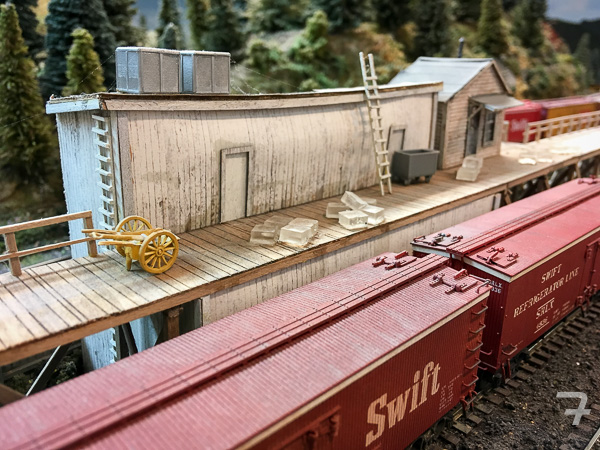
Moving to track-5 we pulled our cleaned reefer string to move them to the icing dock on track-1. We set our third timer for 40 minutes giving us 2 fast clock hours for icing and chilling. Pulling off the icing track, it’s back up the ladder to track-4 to pick up the loaded box car for door-6. Coupled up we move West down the ladder to track-3.
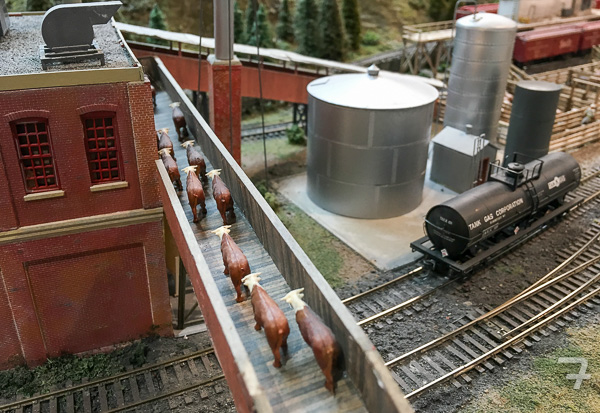
We pick up the loaded tank car and empty box from door-5, then out to the ladder again, backing East to drop the box and tanker against the caboose on track-4 and cut away. We then spot the loaded box we had keep near the engine at door-6, on track-3.
Stepping back to asses our progress we find we have spotted the entire cut of cars we brought from Hoyt Street Yard. It’s now time to build a cut for the interchange. Checking our timers we see that our stock cars have been unloaded and the other timer for the loading dock has expired so the 4 reefers on track-2 at the plant are also ready to be pulled. The interchange track will hold 8 cars, so we back down to track-4 and pick up the tank car of tallow. Next it’s over to track-2 for all three empty stock cars. We also grab the 4 loaded reefers.
Once we had everything on track-2, we had our cut of 8 cars. Pulling up the spur to the company phone and after checking our timetable for scheduled traffic we called the dispatcher to ask if we could have time and track to pull out onto the main and drop our string onto the double ended siding for pickup.
The dispatcher gave us track time after passage of a scheduled freight. We waited 15 minutes for the freight to pass, notified the dispatcher, then pulled onto the main and made our backing move to the siding. Surprised, we find a new cut of cars awaiting us. You can imagine our movements, making the car exchanges along with the time it took plus returning to the plant siding with a new string of cars.
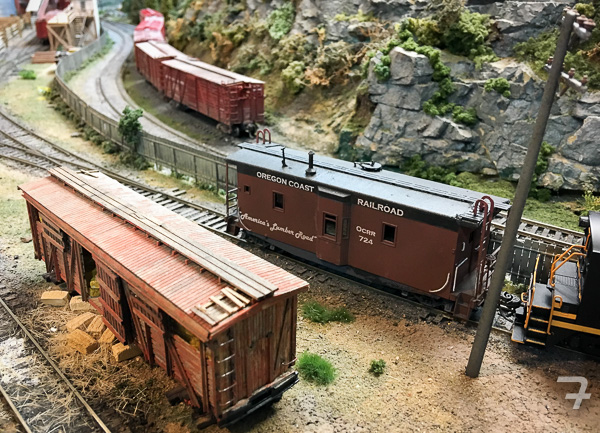
We have now completed one servicing of the plant. The new string of cars picked up from the interchange brought 4 empty reefers and 4 loaded stock cars for us to position as our shift continued. And so it goes, we start another cycle of cleaning, chilling, loading, unloading cattle at the pens, as well as spotting supplies for the plant, and removal of byproducts. The process varies each cycle, dependent on the flow of cars to and from the plant. For instance we received 4 loaded stock cars this time and we have only 3 unloading shoots, so we will have to watch our timing since reefer loading and stock unloading happen on the same track. This variety of movement, timing of processes, masterful placement of service tracks at the plant make this a rich, challenging, and most sought out assignment on Mat’s railroad.
A big industry can be the main theme for a railroad when you are cramped for space. Mary and I were busy for over 3 real time hours servicing the plant. The randomness of cars received required a different operating plan to keep the product flowing from the plant on schedule. So a Swift Packing, cement, automobile, glass plant, or other big industry, with a realistic operating strategy and a few staging tracks can keep a small crew busy in an enjoyable and challenging way for hours. Big industries can be fun and that might be all that you need!
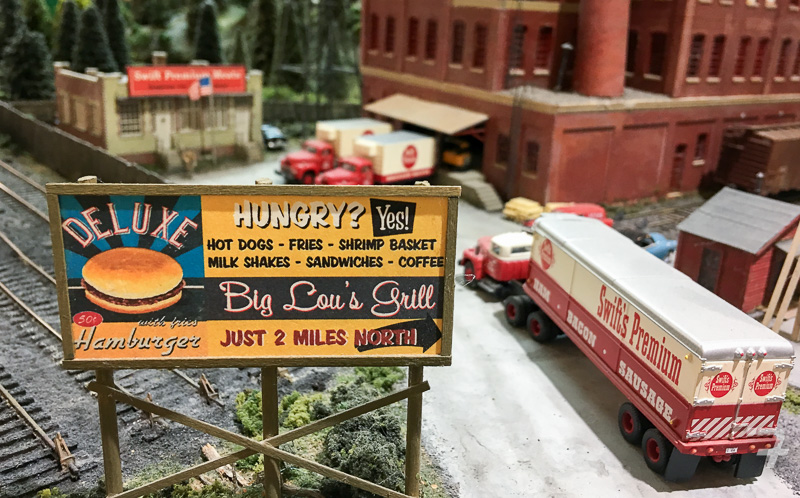